
Friday, September 17, 2010
Public Service Announcement

Thursday, September 9, 2010
I Can't Hear You
![]() |
Handspun sorted by color - Sept 2010 |
I decided to comfort myself by getting out the three full tubs of my handspun yarn to see if I could put together something to weave a shawl with - since my loom is standing empty for the moment.
I spread out the contents of the tubs, and separated everything by color in the middle of the living room floor. I thought if I got it all out, maybe some of it would speak to me and tell me what it wants to be.
Well, it is still there. I must be deaf.
Sunday, August 22, 2010
It's Not Easy to Be Square
Since I have never woven an overshot project, I decided I should weave a sample just to try the structure out. So, I picked out a design from the book Weaving Designs by Bertha Gray Hayes.
I looked through my yarn stash to see what I had on hand that would work for my little sample and came up with 8/2 cotton. I found several different cotton possibilties for weft.
![]() |
3/2 Cotton Weft |
Next I tried two strands of 5/2 cotton in blue. This was better, but still not square.
.jpg)
.jpg)
I decided to give these suggestions a try.
I am still out of sync, rhythm wise, but I am not sure you can ever really get a rhythm in an overshot pattern. The treadles are constantly changing and the shuttles are changing as well. I suppose time will tell about that.
Now I wish I had made that sample warp a little longer.
Tuesday, June 29, 2010
Adieu Knitwords

This was a fabulous magazine for machine knitters. It contained fashionable sweaters for all ages and machine types featuring many techniques. It was a labor of love for the publisher, Mary Anne Oger. The love showed in every issue. I have them all, and refer to them every time I make a sweater on the machine.
The limited good news is that Mary Anne plans to be available for seminars. I hope she will continue to design and publish. She has so much talent and so many creative ideas for machine knitting.
Machine Knitters have so few resources left. For magazines, we have exactly two - Country Knitting of Maine News and Views and Machine Knitting Monthly from the UK.
I urge machine knitters everywhere to support the remaining publications. I would hate to loose them too. We need inspiration for the machine knitters today and those to come.
Thursday, June 10, 2010
First Warp for Ellie's Loom

The first warp is one that I had been planning for my 4 harness Le Clerc. It is yet another project from the Fall 2009 issue of Handwoven Magazine. The "recipe" is on page 44 and is titled "One threading, four patterns, four towels". I had already dyed the contrasting yarns so decided to proceed as planned. This is my fourth project from that issue of Handwoven, and I have more planned. (This may be the best issue ever)
The towels are huck variations. They appealed to me because huck is a new weave structure to me (most structures are since I am only a beginning level weaver), and with four different towels on the same warp, the bore factor should be conquered.
Learning to get along with Ellie's loom has been challenging. I think anytime a weaver deals with a new loom there is a lot to learn about how to get along with it. Everything is strange. The braking system, where to tie up the harnesses out of the way to thread, how to wind the beam where to tie the lease sticks and the list goes on.
Things went pretty smoothly until I started tying up the treadles. The Herald Loom was shipped with wire tie ups, and when I got the loom it had about eight - not enough for my project.
The wires that were in treadles showed signs of being bent with pliers. I got suspicious that Ellie must have had big problems with the wires jumping out of the holes in the lams. Perhaps this is the reason the loom has never been warped.
I researched on Ravelry and Weavolution and found out that indeed, the big complaint about Herald looms is the wire tie ups. Other weavers hated the loom because of the wire tieups. They experienced lots of problems keeping them attached to the lams. Another big disadvantage of the wires is that the treadle height cannot be adjusted, and since the treadles sit on a slant, the back wires or ties are necessarily shorter than the front one's.
Based on this information, I decided that I would most likely change out the wires for ties. I started researching my options. Texsolve cord was recommended. My investigation into it revealed I would have to spend about a hundred dollars to get enough cord to make every connection on the loom. At that point, I was not going to invest a lot of money in a loom that perhaps would not even work, so I needed a cheaper solution than Texsolve.
So, I went to my trusty references from Peggy Osterkamp. Peggy is a total genius. She knows everything about weaving. Her books cover absolutely every problem and question that I have ever had about weaving. I think any weaver with no support needs all of her books.
Peggy recommended tying up treadles with a snitch knot and cords. That is what I did but I used shoe laces for the tie cords, and some nylon cord for the snitch knot section.
I cut a length of cord that is about 10 inches long. I threaded a pony bead onto the cord (to prevent the knot from pulling through the hole), then folded the cord in half and tied a double overhand knot in the two ends. Next I took the loop and let the bead slide down to the knot. I threaded the loop through the hole in the treadle and made a snitch knot that I put my shoe lace ties through. I then adjusted the height of the treadles, looped the end of the shoe laces like the first half of a bow and the treadles were tied up.
After correcting a few threading errors, I am finally weaving. I have employed my poor man's temple for the waffle weave - alligator clips, cord and fishing weights!
Weaving is proceeding. I think I am going to love the loom and I sure love weaving in the airconditioning as opposed to my old studio in the unairconditioned garage.
Monday, May 31, 2010
Ellie's Loom

Sometime probably in the late 70's or early 80's there was a weaver named Ellie who bought a new 45 inch 8 harness Herald loom with a sectional beam. I am sure Ellie dreamed of all the wonderful things she would weave on that loom.
Life must have interfered, because she never go around to weaving on her new loom. It never had a warp.
This year, Ellie, whose memory is failing, moved to assisted living. The unused loom remained behind, stored in a garage with only rats and mice for company. The harnesses collected a little rust.
Ellie's close friend and neighbor began the hard task of cleaning out Ellie's house. The loom went up for sale to another weaver.

Over the last several years, I have been teaching myself to weave. When I started, I thought I would never get a 4 harness loom threaded properly. I marveled that anyone would ever want more harnesses.
However, time in the chair has cured most of my early problems with crossed threads and missed headles. So I decided that if a loom appeared with more than 4 harnesses and if it were inexpensive enough to get passed my strong tightwad nature, I would buy it.
I was at knitting group one day talking about this to some other weavers, and I told them that I was convinced my new loom would find me.
Then, over a week ago, there was a posting to both Weaver's Guilds that I belong to that there was an 8 harness loom for sale. The price was right but I hit delete on the emails because I just had no time to investigate the loom. I was going out of town for several days so the timing was just all wrong.
My friend Kay, of Cordova Studios, also knew that I was looking for a loom, so she kindly forwarded me the email announcement which I saw for the third time. I hit delete. I was just too busy to look into it.

The loom had not been sold to my surprise. No one had even looked at it. When I saw it, I knew my loom had indeed found me.
It took me a day to get it cleaned up. My husband has adjusted the brake. I think it is ready to warp.
I am now re-reading all my weaving publications, paying attention to all the new possibilities that 8 harnesses bring. I think it will keep me busy for a long time.
Now to get a warp on it!
Wednesday, May 19, 2010
Basketweaving - Not the Underwater Kind

Today my Spinning Buddies, the Texas Twisters met at Nancy's house to learn to make a Spinning Basket. This basket is perfect for wool and even has a lazy kate built in as well as a tool holder and a small basket for trash or maybe hand cards or wool combs.
Nancy had everything well organized. We started by measuring all of our materials. The first photo shows Laurie and Joanne working on measuring and cutting the reeds.
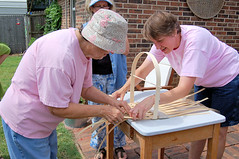
Then we wove a couple of reeds on each side of the handle to get it stablized and centered. Finally we wove enough reeds to complete the bottom of the basket. Then we checked to be sure the corners were square.

As we got higher up the sides, we added in some colored reeds to make each basket our unique work of art. No two are alike and each is beautiful.

Here are photos of some of the baskets as they were at the end of the day. Unfortunately, I don't have photos of all of them.
First is Sharon with her basket. She used red and blue reeds in her basket.



We still have to add the upper basket on and finish the top edges. There is also another small tool basket to make that is attached to the side near the handle.
I hope we get to finish this next week. It is going to be beautiful and so much fun to use!
Sunday, May 2, 2010
Dyeing without a Dyepot



Sunday, February 28, 2010
Grrreat Tiger Wool gets Gold!

Sock blanks are lots of fun to dye, but the knitted results are often not predictable unless the blank is painted in broad stripes. That is, unless the blank is dyed using a method I read about in the Grrreat Tiger Wool Experiment group on Ravelry.
Blanks dyed using this method have a predictable thin stripe of one color with other colors between the stripes. This is achieved by painting one side of the blank in a solid color, and the other side can be painted in a different color or several colors.
This photo shows my Go for the Gold Socks in progress on top of the dyed sock blank. Notice the blue on the blank has turned into thin regular stripes on the socks.
There are many other possibilities with this method. Faux fairisle can be put on the non-stripe side, or you can have the faux fairisle interrupt the striping for a ways. There are lots of photos in that Ravelry Group to get more ideas from. Check out the thread called Experiment #6
The distance between the stripes is determined by the width of the blank and the width of the solid area. To get a complete stripe, the solid area needs to contain a complete round of sock yarn. For me, this is just under 30" for a 60 stitch sock. Thirty inches translates into 40 knitted stitches at the stitch and row gauge I used to make this blank, so, my solid area needs to be 20 stitches wide down one side of the blank to get one solid row. The wider the blank is, the more rows of knitting I have between the solid stripes.
Now that I know the math, my next sock blanks will be machine knitted with this dyeing method in mind so I can get wider spacing between the stripes.

I dyed another blank at the same time and have those on my needles now. They will be knitted in the Skew Pattern from Knitty Winter 2009. Skew should show off this type of sock yarn to great advantage.